RIFTEC is friction stir welding
Here you can learn everything about friction stir welding. We have been friction stir welding for over 20 years, first in research and then for industry. Throughout Germany, RIFTEC has the most experience and expertise in friction stir welding. With our six state-of-the-art FSW systems, we offer our customers almost unlimited possibilities in component size and geometry. Please learn more about our possibilities.
I regard RIFTEC as a pioneering company and one of the very first companies to develop the Friction technology commercially in Germany. (…) Axel and Alex `pinned their colours to the mast`- they championed the technology when others were unsure.
Wayne Thomas, inventor of friction stir welding at TWI in Cambridge
The process is remarkably simple. A special rotary tool runs along the joint between two workpieces, with the shoulder of the tool riding on the edges of the joint. The rotation and the pressure exerted generates heat by friction, which plasticises the material. On its path along the joint, the tool stirs the material of the two workpieces and compresses it at the same time. The result is a very solid joint.
Schematic representation of the friction stir welding process
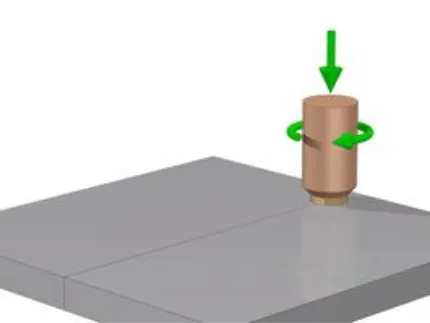
Wear-resistant tools create frictional heat and exert pressure on the joining area. The fixing of the components and a solid base ensure that the horizontal and vertical process forces are absorbed.
The friction between the rotating tool and the material gives rise to the heat necessary for plasticization.
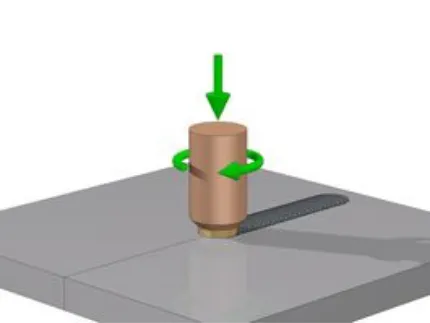
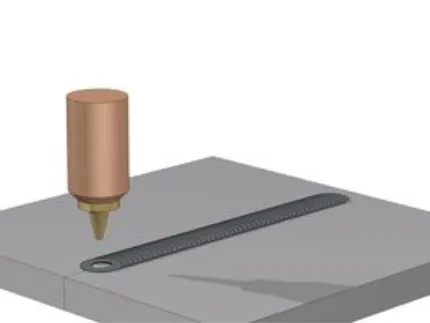
The advantages of FSW:
- Strengths of 80 - 100% of the parent material
- High degree of weld-strength
- Gas- and pressure-tight
- Little distortion
- Usually no pre- or post-processing required
PLUS:
- Very eco-friendly welding process without shielding gas or filler materials
- Low carbon footprint due to the use of green electricity