Welding processes for aluminium: A comparison
Which is the best welding process for aluminum?
Again and again we are asked whether FSW is really the best welding method for joining aluminium. Several other methods have been established on the market for much longer. In addition to various hybrid processes, TIG, MIG, MAG, laser beam welding, electron beam welding are much better known. We decided to work with friction stir welding 20 years ago. To check whether we are still correct with this decision after all these years, we have called for a comparison of welding processes and asked: What are the advantages and disadvantages of these methods? Is friction stir welding really better or are there equivalent processes? Are there any welding processes that could also be interesting for our production in terms of quality and process reliability? We are addressing these questions sin our current project - a comparison of the most important industrial welding processes for aluminium.
The welding process test
At RIFTEC, we offer friction stir welding, TIG welding and MIG welding in-house. For our process comparison, however, we used friction stir welded profiles from HAI in Ranshofen, which are manufactured there in series with the double spindle. In addition, we needed sample welds of other welding processes. We were able to win a total of 11 external, independent and well-known companies as well as institutes to participate in the process comparison, whose results were included in the comparison. The joining task for all of them was the welding of aluminium hollow profiles made of EN AW 6063 T6 with a weld penetration of 3 mm.
The Experimental Setup: This is how we checked the welds
The quality oft he seams shall be testet on the basis of the common test methods for welds on taken samples:
- Optical quality inspection of the weld seams, i.e., visual inspection
- At RIFTEC, certified visual inspectors inspect the optical quality of the weld seams.
- Metallographic examination
- For the metallographic examination we take samples from test welds to create crosssections, which are etched in the laboratory. Pores, cracks or other irregularities in the seam area can be detected under the microscope.
- Tensile test
- For the tensile tests, we take standardised specimens with a defined cross-sectional area. These are stretched uniformly until they break. Thus the yield strength, tensile strength and elongation at fracture can be determined.
- Carbon footprint
- Using an established database, the consumption of materials such as filler materials and shielding gases, as well as the average electricity consumption are converted into an carbon equivalent.
We let these welding processes compete against each other in the test:
In addition to friction stir welding, we have selected four other processes for this welding comparison. All these welding processes are industrially recognised and are among the most important welding processes for aluminium.
Friction Stir Welding (FSW)
Friction stir welding is a pressure welding process. It does not require any filler materials or shielding gases. No seam preparation is necessary because the oxide layer does not interfere with friction stir welding. The material at the joint is not melted, but merely plasticised. Thus, relatively little distortion is introduced into the component.
Laser MIG Hybrid Welding (LMH)
Laser-MIG hybrid welding combines two processes of welds, as the name suggests: laser and MIG welding. The advantages of both processes are utilized. Weld seam preparation can be reduced, while at the same time the welding speed is quite high. This results in good economic efficiency.
Laser Beam Welding (LBW)
Laser welding is particularly suitable for high welding speeds and narrow seam shapes that are to be joined with low thermal distortion. In laser beam welding, the metal is heated above the melting temperature. A shielding gas prevents an oxide layer from forming on the seam.
Metal Inert Gas Welding (MIG)
MIG belongs to the group of gas-shielded welding, more precisely to arc welding, and is thus a fusion welding process. The shielding gas used is an inert gas that does not react with the molten metal. The electrode acts as a filler metal in MIG welding. Pre- and post-processing of the joint is quite time-consuming, but this makes welding with MIG all the faster.
Tungsten Inert Gas Welding (TIG)
TIG is a welding process with shielding gas using a non-consumable electrode made of tungsten. Inert gases such as argon or helium in pure form or their mixtures protect the arc. This burns freely between the electrode and the workpiece. One advantage of TIG welding is that almost all metals can be welded with this process.
The metallographic examination confirms the impression of the visual inspection:
Friction Stir Welding (FSW)
No irregularities can be seen, the required weld penetration has been achieved.
Tungsten Inert Gas Welding (TIG)
Even with TIG, no irregularities can be seen, and the required weld penetration has been achieved.
Laser MIG Hybrid Welding (LMH)
With this laser process, the weld penetration is greater than required. Cracks and flaws are clearly visible. However, the seam quality is better than with LBW.
Metal Inert Gas Welding (MIG)
In MIG, most of the seam is above the surface, the seam sometimes shows strong porosity.
Laser Beam Welding (LBW)
With this laser method, too, the weld penetration is greater than required. Here, too, there are clear cracks and flaws.
Tensile Testing
According to the metallographic examination, the results of the tensile specimens of FSW, TIG, MIG and LMH are quite similar in quality. LBW performs significantly worse in comparison and exhibits a lower strength value.
Carbon footprint
In welding, CO2 emissions are mainly caused by the consumption of filler materials, shielding gas an electrical energy. The energy consumption in the current welding comparison is lowest in MIG welding, but a lot of filler material is used here, which has negative impact the CO2 balance. With LMH, the energy consumption is very high due to the high process effort. Both laser processes require filler materials and shielding gases. Only with FSW does the CO2 footprint result solely from energy consumption. This is significantly lower than with the laser processes. Friction stir welding produces the lowest CO2 footprint of all the processes in this comparison. RIFTEC has been using CO2-neutral electricity for many years, so our footprint is almost zero.
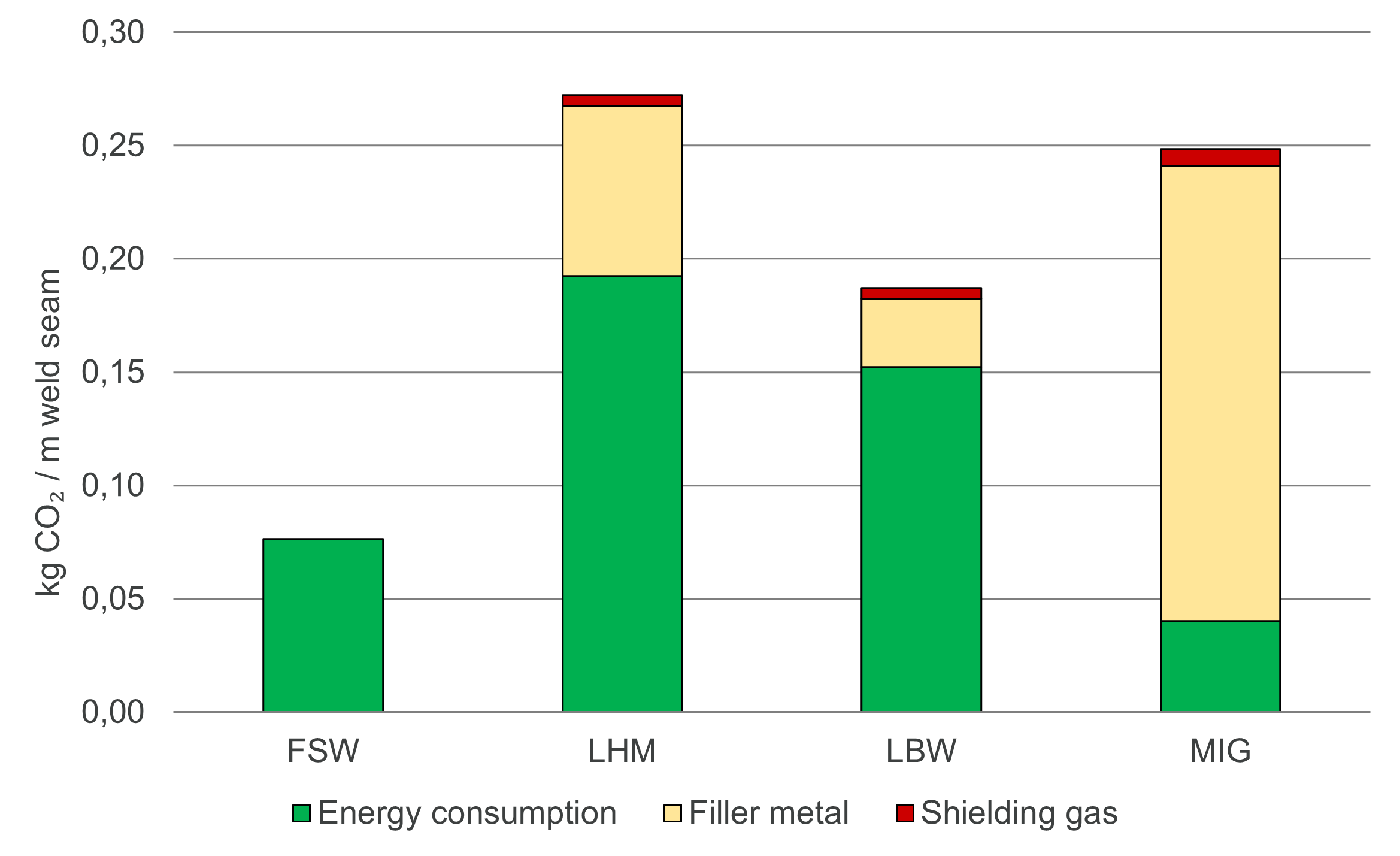
Conclusion on our comparison of welding processes
In this comparison of welding processes, friction stir welding performs best terms of visual inspection, metallographic examinations and sustainability. Friction stir welded seams have a quality very close to the base material. The carbon footprint of FSW with green electricity is approaching zero. Looking at the metallographic results and tensile strengths, laser MIG hybrid welding is almost equal to FSW, but loses out to friction stir welding due to the high process effort - which, however, was not investigated further here. Laser beam welding delivers the poorest quality results.